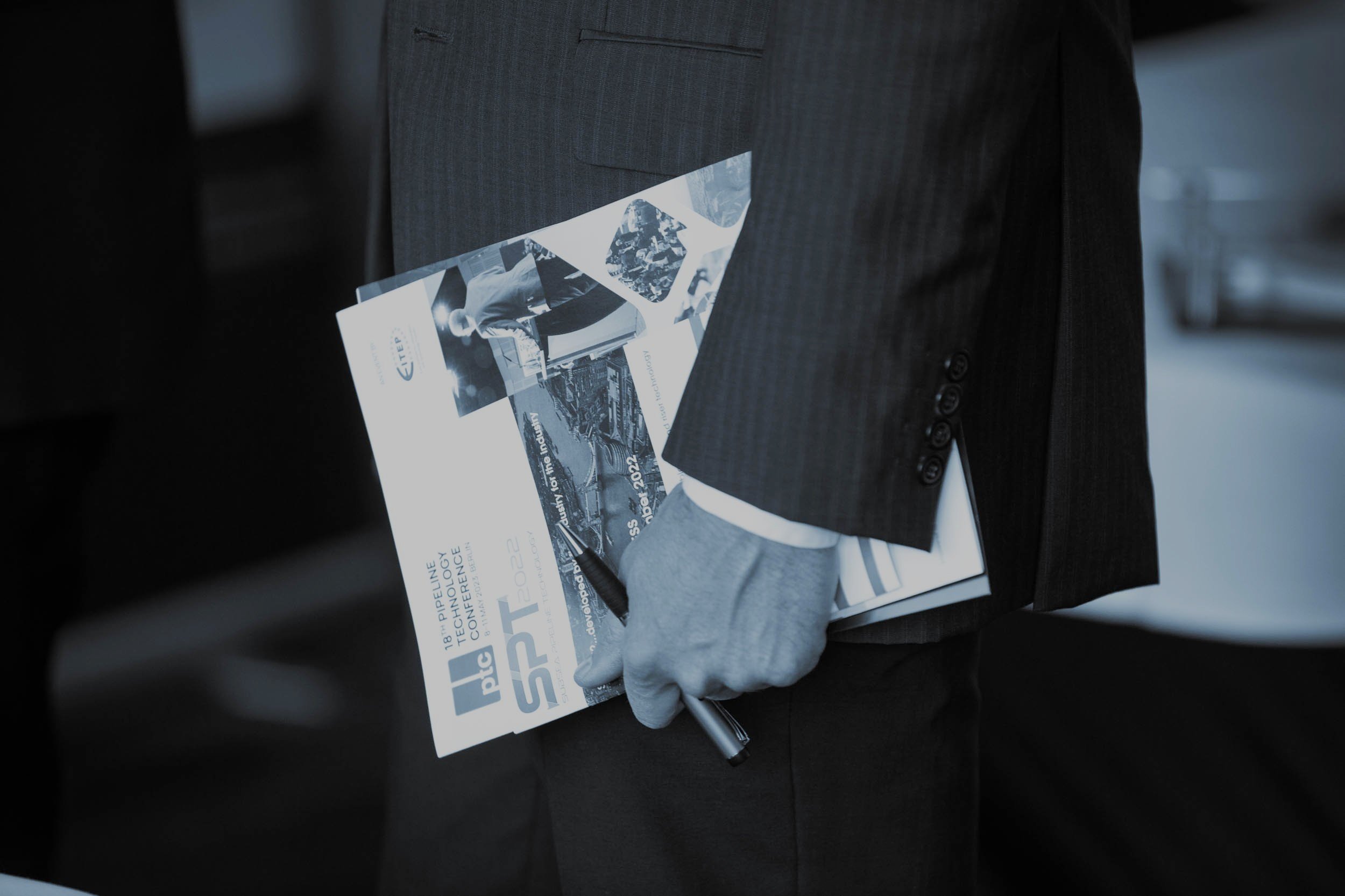
Agenda
SPT 2023 Congress
Leonardo Royal Hotel
London Tower Bridge
DAY 1 THURSDAY 21 SEPT 2023
Registration and coffee
08:00
Welcome to SPT 2023
Steve Woolley, Director, SW Conferences Ltd
09:00
Welcome from the session chair
Andy Studman, Principal Pipeline Engineer, Shell International
09:05
SESSION 1: GLOBAL MARKET OUTLOOK
Global offshore energy outlook and implications for the offshore pipeline sector
• Review of the oil & gas and the renewables market
• Impact of oil price on the offshore pipeline sector
• Geopolitical events and pipeline trends
• Opportunities from offshore wind
• Future forecasts
• Potential bottlenecks - are newbuilds likely?
Mark Rae, Director – Research and Analysis, S&P Global Commodity Insights
09:10
Keynote address A contractors view of the global offshore pipeline market
• Market analysis and impact on the contractor community
• Operating in a transitioning market, meeting new demands
• New approaches and solutions to achieve enhanced cost efficiencies and greener operations
• A look to the future
Pieter Heerema, President, Allseas Group
09:35
Keynote address An holistic view of the low carbon value chains
• The scale of the challenge
• CO₂ and hydrogen pipeline projects
• Low carbon hydrogen project, UK
Asbjørn Haugsgjerd, Vice President for Projects, Equinor
10.00
Networking break
10:25
SESSION 2: DEVELOPMENTS IN HPHT TECHNOLOGY AND PROJECT REVIEWS
Ensuring Reliable Pipeline Transport for 80% of Southern Africa’s Crude Import
Speaker: Pieter Swart, Director and Pipeline Authority, SeaLeopard Engineering
Author: Pieter Swart, Director and Pipeline Authority, SeaLeopard Engineering
10.50
-
South Africa’s Main refineries are located near Durban and import around 80% of the country’s crude oil through an aging 48“ offshore pipeline. The concrete weight coated pipeline lies on the seabed attached to a Single Point Mooring (SPM)
With a length of approximately 2.5km, this production critical pipeline ran in till 2018 unburied from the SPM to the beach through a zone of active seabed.
During regular surveys since 2006 it was discovered that the seabed is heavily scouring with as a result the progressive self-lowering and overstressing of the pipeline over a section of ~800m. This fact, combined with the ongoing internal corrosion, raised concerns if the planned service life could be met. On this basis an analysis of the structural reliability and other risks was executed by Shell with the aim to ensure the remaining lifetime and come up with solutions to mitigate the risks and maximize pipeline lifetime extension.
Fenris HPHT 50 km collaborative pipeline design for through life In line Inspection, and zero platform personnel risk
Speakers: Toby Bird, Principal Engineer, Subsea 7 and Paul Westwood, Principal Engineer, ROSEN
Authors: Toby Bird, Principal Engineer, Subsea 7 - Paul Westwood, Principal Engineer, ROSEN
Frank Bijster, Senior Sales Manager – North western Europe & Israel, ROSEN
11.20
-
This paper will present how a flowline and topsides have been designed to reduce CAPEX costs to while ensuring the safety and integrity monitoring of the flowline based on material selection. Subsea infrastructure, and in particular pipelines, need to be carefully evaluated for throughput piggability point of view. This is to ensure that the pipeline will satisfy the regulatory requirements for integrity monitoring. With deeper wells come higher pressures and temperatures, which often leads to exotic material selections with increased wall thicknesses and therefore higher project cost. Minimising CAPEX is repeatedly the aim of the pipeline design team whilst ensuring safety is maintained throughout the pipelines design life. Located in the Norwegian North Sea, the unmanned Fenris platform is approximately 50 km north of the Valhall field centre and has shut in wellhead conditions of 862 bar and 170°C. The pipeline system has been designed in 2 sections that complies with the DNV guidance for HIPPS protected pipelines. This was achieved by very close collaboration between the pipeline EPCI contractor, Subsea 7, and the proposed In line Inspection provider, ROSEN. The removal of the valves and PLR connections from the Fenris platform resulted in a major cost and weight saving for the platform design. This pipeline design also totally removed the need for personnel to access the unmanned Fenris platform for pipeline inspection operations on the 50 km carbon steel pipeline.
Development of high-temperature field joints for PiP
Speaker: Aurelien Damour, Innovation Project Manager, ITP Interpipe
Authors: Aurelien Damour, Trung PHAN and Emmanuel PEREZ, ITP Interpipe
11.50
-
An operator in West Africa has requested ITP to improve its field-proven rapid J-lay Pipe-in-Pipe (PiP) for temperatures higher than 100°C or even 125°C.
Currently, ITP Interpipe’s offshore field jointing system for PiP (more than 400km already in operation in West Africa and North Sea), uses a fast-curing polyurethane resin for load transfer across the field weld during J- or S-lay installation. This resin has the benefits of being a fast-curing material that will have little impact on the barge laying rate (3.5km/day achieved installation rate) but it has a limitation in term of design temperature in sea environment.
To increase the capacity of this field-proven field jointing system, an alternate design is under qualification using a fast-curing grout specifically developed for this application. The use of a grout as several advantages compared to a resin: its Young’s modulus is more 10 times higher than polyurethane resin, and stable over the temperature windows from 4°C to 125°C. Also, the grout thermal expansion coefficient is similar to the steel thermal expansion coefficient resulting in limited thermal stress in the field joint in operation.
This paper presents the progress of the qualification of this upgraded field-joint system.
The first step of the qualification was to develop a grout formulation to fulfill the technical requirements of the load-transfer material: curing time of ~5min, intrinsic mechanical properties suitable with installation and operation loads. The new material was tested following standardized grout testings to confirm its ageing properties. In parallel, prototypes were fabricated and tested to confirm mechanical behaviour of the grout under high bending strain (up to 0.4%) and with alternate traction/compression cycles. Another important part of the qualification is to develop a process and associated equipment for mixing and injecting the grout on the laying barge offshore.
The main challenge is the grout curing time that excludes most of the standard grout mixing and pumping process: the operational risk is too high to pump the grout already accelerated, therefore a configuration has been developed with the grout accelerator being mixed after the pump. The paper will present the status of the qualification with the results of tests already done and the remaining technical uncertainties to be covered.
Further developments of the Fenja ETH-PIP project
Speaker: Antoine Marret, Project Engineering Manager, TechnipFMC
Authors: Antoine Marret, Piotr Malota and Torgeir Helland, TechnipFMC
12:20
-
The Fenja Field is located offshore mid-Norway at a water depth of approximately 324 m, and consists of two separate hydrocarbon accumulations, the Pil and Bue reservoirs. The reservoirs’ fluid properties are challenging, and Neptune Energy concluded that the Electrically Trace Heated Pipe-in-Pipe (ETH PIP) Technology would be the best technical and economical option to develop and produce the reservoirs. This paper presents a high-level overview and outcome of the development, industrialization, fabrication and installation of the TechnipFMC’s second generation ETH-PiP for application to the FENJA field development. It also presents the outcomes from the ETH system performance test conducted during the final commissioning of the system. The new ETH-PIP v2.0 has higher electrical rating of 3.8/6.6kV to overcome the specificities of the FENJA field development including the long tie-back distance of 38km which makes FENJA the longest (and largest) ETH-PiP in the world. The installation was finalized in Summer 2021, with the complete system being connected and tested from the Njord A platform after it returned from refurbishment in Spring 2022. Final commissioning and validation of the ETH-PiP performances were completed early 2023.
12:50
Lunch
SESSION 3: PIPE MANUFACTURER AND SUPPLY CHAIN PERSPECTIVES
Session chair: Venkatapathi Tharigopula, Concept Manager - Trunklines, Equinor
Keynote address Supply chain challenges when considering the future role of subsea pipelines in the energy transition
• Pressures in the supply chains: competition from other steel intensive sectors
• Design challenges presented by CO₂ and H2 and the impacts this has on the supply chains
• What activity is being carried out in terms of preparation and readiness for these challenges
Speaker: Martin Connelly, Technical Director, Liberty Pipes (Hartlepool) Ltd
13:50
Cladtek´s experience and recent developments in the application of Mechanically Lined Pipe / MLP
Speaker: Tiago Kaspary, Technical Authority for MLP & Connectors, Cladtek
Authors: Tiago Kaspary, Eduardo Menezes, Jessica Pisano and Paul Montague, Cladtek
14:15
-
Mechanically lined pipe has been a very competitive alternative to solid CRA pipe or metallurgically clad pipe for offshore and onshore pipelines conveying corrosive fluids, with decades of successful application. Cladtek´s innovative solution of cladding and machining the pipe-ends back in 2004 significantly improved MLP installability by addressing the associated challenge of fit-up with clad girth welds, having become the industry standard. In the years since, Cladtek has created a number of improvements to the product, including the fabrication and installation of the largest diameter MLP in offshore use in Nigeria and the fully lined rigid risers in the Brazilian Pre-Salt. In this paper, Cladtek discusses the history of its MLP in the industry, its understanding on the limits of its application - in particular through case studies and improvements in recent projects, addresses a number of ongoing developments in the fabrication and inspection of this product. Finally, opportunities for new developments are proposed.
Networking break
14:45
SESSION 4: CASE STUDIES ON RECENT DESIGN CONSIDERATIONS
Advances in the approach to on-bottom stability on rocky seabeds
Speaker: Chas Spradbery, Director of Operations and Business Acquisition, Peritus International
Authors: Chas Spradbery, Peritus International Ltd and Terry Griffiths, Aurora Offshore Engineering
15:15
-
It is well understood that traditional on-bottom stability designs are over-conservative for small diameter items such as cables and umbilicals. Furthermore, that when cables are placed on rough or rocky seabeds the traditional methods do not adequately capture the interactions between the cable and the seabed. Therefore, a new approach to cable stability on rocky seabeds has been developed. This approach is contained within a new British standard BSI 10009, due to be published later this year. This presentation will cover the background research leading to the novel approach to seabed stability described within the standard, along with case studies demonstrating how the methodology as been applied in real world situations leading to both cost and risk reductions.
Development of a computational tool to optimise minimum wall thickness of reeled rigid steel
subsea pipelines based on experimental results
Speaker: Dr. Eric Giry, Senior Lead Pipeline Engineer, Saipem
Authors: Dr. Chen Shen, Mamadou Ahmed-Kogri, Dr. Eric Giry, Richard Stableford
and Dr. Diego Pavone, Offshore Subsea Engineering, Saipem
15:45
-
Reel-laying is a long-established method for installing rigid subsea pipelines and has an extensive global track-record. In comparison with J or S-Lay methods, reel-laying imposes large deformations which could trigger failure by buckling, fatigue or fracture. Pipe manufacture and pipeline fabrication are carefully controlled, but each pipe has a tolerance on geometry and materials properties. Saipem performed a programme of full-scale reeling simulations to develop an accurate computational model for use in reeled pipeline design. The reeling simulations included 12m long pipes cut in half with an accurate counterbore machined in one end before welding back together. This creates a union of carefully controlled strong and weak “mismatched” pipes. Materials testing was also performed. FE simulations using parameter-based material model was validated against the full-scale test data. The FE modelling allows the DNV “pipe mismatch failure curve” to be developed into a useful tool in the Pipeline Design Engineers toolkit.
Kristin Sor - Residual curvature method on a Hot PIP exposed to trawl interaction
Speaker: Michele Cerulli, Principal Pipeline Engineer, TechnipFMC
Authors: M. Cerulli, M. Abdullayev, C. Cooper, TechnipFMC - Jonathan Stuart Bracher, Equinor and Pål Foss IKM
16:15
-
The Residual Curvature Method (RCM) has proven to be a very effective method to initiate controlled lateral buckling of exposed pipelines that are installed using reel lay vessels. Most pipelines installed to date that have adopted RCM buckle initiators were single pipelines. However, as the technique has gained maturity, it has started to be used for Pipe-in-Pipe (PIP) flowlines as well. This paper presents a summary of the work undertaken to demonstrate the suitability of RCM for the Equinor Kristin Sor PIP system, which is exposed to trawl interaction and where RCM buckle initiators were adopted to control lateral buckling. Key aspects of the interfaces between in-place design and installation engineering will be presented with particular attention paid to the uncertainties that need to be addressed to demonstrate the robustness of the solution. Along with the usual uncertainties considered in pipeline lateral buckling analyses, for example pipe soil interaction and bottom tension, other uncertainties specific to RCM installation are examined, including RC strains, curvature and RCM section rotation. The results of the assessment are presented, key challenges are discussed and lessons learned shared.
Interactive roundtable session
This session will provide an informal environment for delegates and speakers to come together to discuss and debate those issues currently influencing their business. Each table will be moderated by a leading expert and delegates choose which table to join:
• Opportunities for pipelines in the offshore wind sector
• CO2 pipelines in the energy transition - repurpose or build new?
• Hydrogen pipelines
• Energy security and what role can pipeline projects play?
Chairman's closing remarks
16:45
16:50
Close of Day 1 followed by Networking Drinks Reception
18:00
19:30
SPT Gala Dinner
DAY 2 FRIDAY 22 SEPT 2023
Registration and coffee
08:30
Welcome from the chair
Pieter Swart, Director and Pipeline Authority, SeaLeopard Engineering
09:00
SESSION 5: HYDROGEN’S ROLE IN THE PIPELINE SECTOR
Design levels in offshore hydrogen pipelines
Speaker: Leif Collberg, Vice President – Energy Systems, DNV
Authors: Leif Collberg, Jan Fredrik Helgaker and Erling Østby, DNV
09:10
-
Hydrogen gas as an energy carrier is predicted to play a key role in the global efforts to decarbonize. As part of the hydrogen value chain, pipelines are considered an attractive option for transportation, either for transportation of pure hydrogen gas or as a mixture with natural gas. In this context, both new pipelines and utilisation of existing infrastructure (re-qualification) are possible options. One contributing factor for the push on hydrogen pipelines it its potential ability to accumulate/store gas which is a very tempting aspect when connected to non-stationary generation like solar and wind. One interesting question arise; is there a need for any R&D for hydrogen pipelines with all the statements of “hydrogen ready” pipelines? In the on-going DNV JIP H2Pipe, a design level scheme has been proposed to differentiate designs depending on its maturity and knowledge ranging from low to very high. Today, DNV consider only the level Low, typically covered by AS;ME B31.12, to be sufficiently proven for design which excludes the majority of offshore pipelines. The design levels and the linked concerns will be presented. A discussion of concerns will also be given and the difference between “do not know/lack knowledge” and “not possible”.
• Code and regulation requirements for H2 service
• Operational safety risks and mitigations: hazardous areas, vapour cloud explosion, ESD, risk contours
• Emergency response: shut down and venting
• Hydrogen operations: SCADA, leak detection, visual inspection, testing
• Hydrogen integrity management: pigging, crack detection, repair
Hydrogen pipeline safety and operations – What are the differences from a natural gas pipeline?
Speaker: Colin McKinnon, Technical Director – Technical Consulting, Wood
09:40
10:10
Networking break
SESSION 6: CASE STUDIES ON RECENT INNOVATIVE PIPELINE PROJECTS
Shore-based remote capabilities enable successful isolation and decommissioning of North Sea pipeline
Speakers: Stephanie Craig, Project Manager, TD Williamson and Kenneth Solbjør, Product Manager, Oceaneering
Authors: Kenneth Solbjør, Product Manager, Oceaneering - Gary Anderson, Senior Manager Sales, TD Williamson
Georg Johnsen, Principal Engineer, Equinor
10:40
-
Remotely operated vehicles (ROV) and support vessels are essential to support subsea pipeline operations, including subsea inline isolations. Subsea pipeline isolation operations require robust communication systems to control and monitor tool loading, tracking, activation and deactivation. Typically, the system is hardwired or acoustically linked to the platform or vessel, supported by the vessel ROV. The duration of the isolation will dictate the support vessel time on location. Advancements in remote communication technology in both the ROV industry and the pipeline isolation industry have shown how support vessel dependency in such operations can be eliminated.
This paper covers an actual pipeline decommissioning project whilst keeping the downstream pipeline system operational, all remotely from an onshore location. The solution paired advanced pipeline isolation technologies with a resident, battery-powered, work-class E-ROV system with LTE connectivity. The combination enabled the subsea inline isolation to be performed via a remotely deployed EROV system from an onshore operations center, an industry first. By using the onshore remote operations center, the project team was able to collaborate, control and watch live operations through the remote EROV. The isolation tool communication system interfaced through the EROV allowing the tracking, activation, monitoring and unsetting of the tool subsea, direct from the onshore operations center. Removing the vessel requirement eliminated costs, improved safety and dramatically reduced the CO2 and environmental footprint of the isolation operation.
An innovative approach to simplifying subsea pipeline crossing at open sea using horizontal directional drilling (HDD) technique
Speaker: Suzaini Zainal Abidin, Manager (Offshore Installation), PETRONAS
Authors: Suzaini Zainal Abidin, Helmi Ngadiman and Faizal Shahudin, PETRONAS
11:10
-
This paper summarizes the basic operational steps taken by PETRONAS to complete its first open sea to open sea offshore Horizontal Directional Drilling (HDD) at one of its pipeline crossing locations at KP 83.709 for its newly installed pipeline for project located at Java Sea, Surabaya, Republic of Indonesia. The pipeline is a 12-inch, 110-kilometer gas export pipeline from the “A” platform to Onshore Receiving Facilities (ORF), at a water depth of 5 to 6 metres below mean sea level (MSL). This paper describes in general the construction methodology and operational steps for using the HDD method to cross beneath the 18-inch buried live existing pipeline from open sea to open sea. To comply with the authority regulation, all pipelines located less than 13 metres below sea level and within shipping channels must be buried at a depth of two metres below the seabed, this HDD method was chosen instead of the typical subsea pipeline slipper crossing. The crossing has been carried out in a single drilled section measuring approximately 350 metres in length from the entry point (at Drill Barge, Barge #1) to the exit point (at Receiving Barge, Barge #2) located offshore. The clearance requirement for the existing 18" pipeline (buried 2 metres below seabed) is between eight (8) and ten (10) metres below the pipeline's bottom. The entire drill string length is approximately 610 meter including a 130 meter long tail string coated pipes with 30mm thick concrete (at both side) which was pulled and laid on the seabed before Pipe lay Barge came to pick-up, tie-in and continue laying towards onshore.
Despite numerous challenges and limited experience, the project was completed on time, within budget, and with no LTIF or TRCF. This paper will provide a guideline for future similar project undertakings on the selection of marine vessels and equipment, the overall safe operation, and the efficient method to execute the project successfully. Commonly, the HDD operation is performed on the land side for pipeline shore approaches or pipeline crossing purposes to avoid an open-cut method across any existing facilities/utilities (road crossing, building, river etc). However, in this project, the HDD operation was performed at the open sea crossing the existing oil pipeline.
The path to replacing conventional pre-commissioning for the BM-C-33 gas export pipeline
Speakers: Jean Malnory, Senior Engineer, DNV and Odd Reidar W. Boye, Technical Manager - Subsea, IKM Testing
Authors: Jean Malnory, DNV - Odd Reidar W. Boye, IKM Testing AS - Stein Rimestad, Equinor
11:40
-
The BM-C-33 gas export pipeline (GEP) is one of the deepest large-OD pipelines under development. The offshore field is located 200 km off the Brazilian coast, in 2800 m water depth in the southern part of Campos basin. It was early identified that water filling, system pressure testing (SPT) and subsequent dewatering would become operationally challenging and also have a significant cost impact.
The BM-C-33 project team has therefore with support from DNV assessed the opportunity for obtaining an equal - or better - integrity level without performing SPT for its GEP. The project has adopted the methodology developed as part of the Replace JIP and the resulting guideline issued in 2020. The JIP REPLACE guideline is based on DNV-ST-F101 allowing replacement of the SPT of a pipeline system with alternative means while keeping an equal or better safety level.
This paper will present the REPLACE methodology adopted by the project; more specifically, what were the motivations for BM-C-33 and the implementation process - including checking consequences of the system design and the added safeguards through a semi-quantitative risk assessment. This semi quantitative risk assessment demonstrates that these proposed safeguards ensure an equivalent or better safety level.
Development of the Pre-commissioning (PCO) Philosophy for BM-C-33 will thereafter be presented, outlining essential conditions, assessments and specific solutions implemented to conform with the REPLACE guideline. A comparison with a conventional PCO solution will further be made, identifying the main upsides with REPLACE for BM-C-33
In total, the paper highlights how the REPLACE methodology can represent a potential gamechanger for certain projects. The new methodology offers significant advantages particularly for large-OD, long and deep pipeline systems. Avoiding water filling may provide a long range of upsides with regards to offshore operations, environmental impacts (chemical usage), equipment spreads and in-field logistics.
12:10
SESSION 7: FLEXIBLES
Lunch
Session chair: Carlos Scilia, Head, Rigid Pipe and Riser Design Group, TotalEnergies
Best practice - flexible pipe corrosion assessment
Speaker: Svein Are Løtveit, Senior Advisor and Founder, 4Subsea
Authors: Svein Are Løtveit, Senior Advisor and Founder, 4Subsea and Morten Eriksen, Senior Advisor, 4Subsea
Arne Dugstad, Chief Scientist, Institute for Energy Technology
13:10
-
This paper presents a best practice for corrosion assessment of flexible pipes. The best practice is based on the two flexible pipe corrosion monitoring (FPCM) projects. The objective was to understand the annulus chemistry and the corrosion mechanisms and to give best practice guidance to integrity assessment and monitoring. The FPCM-II project included the following partners:
• 4Subsea, Project management
• A/S Norske Shell, Okea AS,
• Equinor ASA and Chevron U.S.A. Inc, Industry sponsors
• Institute for Energy Technology (IFE), R&D partnerCorrosion of the steel armour wires is one of the most important mechanisms limiting the safe service life of flexible pipes. In an oxygen-free annulus with water present, confinement combined with large steel areas and low water volumes normally leads to very low corrosion rates. In some upset conditions, the corrosion rate may be high, and the best practice gives guidance for evaluation of these. The FPCM II Best Practice also considers various corrosion scenarios, supporting tools, evaluation methods and topics relevant to risk evaluation.
Corrosion resistant dynamic flexible pipes for high pressure CO2 production, injection, and storage
Speaker: Danny Krogh Nissen, Technical Manager - Development and Qualification, NOV Flexibles
Authors: Danny Krogh Nissen, Technical Manager, Development and Qualification, NOV Flexibles Denmark and
Kasper Lund, Metallurgist, Materials and Testing, NOV Flexibles Denmark
13:40
-
When operating in high CO2 applications, unbonded flexible pipes reinforced by conventional carbon steel are exposed to the risk of stress corrosion cracking (SCC), resulting in integrity failure, or significant service life reduction. This is relevant for conventional offshore O&G production and the emerging field of carbon capture, utilization, and storage (CCUS). The corrosion resistant flexible pipe provides an extension to the safe zone on conventional flexible pipes by eliminating the SCC risk and securing full-service life, while in all other aspects behaving as a conventional flexible pipe. The objective of this paper is to present the qualification evidence for flexible pipes with a highly corrosion resistant, high strength steel grade replacing the carbon steel armour wires with identical wire profiles and verifying the use of consolidated flexible pipe methodologies and processes. An extensive risk assessment has been performed, resulting in +65 individual identified threats, endorsed by Independent Verification Agency, covering dynamic HPHT deep water applications. A substantial amount of material qualification has been performed, showing suitability within; CO2 stress corrosion cracking, sulfide stress cracking (SSC), crevice corrosion and hydrogen embrittlement, pitting resistance, biocorrosion, and much more. A complete prototype pipe has been manufactured, and full-scale tests have been successfully performed, showing excellent compatibility with existing manufacturing processes and design methodologies. This paper will present the outcome of the FMEA sessions, summarizing the outcome of 5 separate qualification plans leading to full-scale product validation
Does rapid x-ray technology hold the key to transforming pipeline integrity?
Speaker: Barry Marshall, General Manager, Aisus
Authors: Barry Marshall, General Manager and Jan Stander, Managing Director, Aisus
14:10
-
The energy industry has for many years been seeking solutions to the complexities of integrity management of pipeline assets. Unbonded flexible risers have been a particular difficulty, and the introduction of fully bonded composites creates new challenges for integrity management. Until now, the lack of a practical and effective inspection method has forced integrity management to be based on engineering models and statistical predictions using extremely limited inspection data. Inspection data from a small sample area of a pipe system has had to be assumed to be representative of the overall pipe condition for integrity management. The data is used to predict the overall condition as well as the life expectancy of full complex pipeline networks, by statistical analysis rather than actual evidence. Additionally, new pipe designs and complex pipe structure such as Unbonded Flexible Pipe and Thermoplastic Composite Pipe (TCP) have been introduced to the market. These have essentially been ignored for inspection because regulators have deemed them un-inspectable, as no technology existed to inspect these new pipes due to their multi-layered complex constructions of non-metallics. This white paper explores how new high-speed x-ray technology is transforming the industry, making it possible for the first time to scan the full length of spoolable pipes while providing almost microscopic-level insights. This enables manufacturers to provide greater assurances and quality control to clients and gives operators a traceable digital record for the full lifecycle of the pipeline. Any changes to the pipe condition can be detected and monitored, providing data that gives confidence in the life of asset predictions, as well as enabling feedback to designers, manufacturers, and regulators. The end result is a dramatic reduction in Risk and an elimination of in-field failures.
Inspection and cleaning of flexible riser annulus vent ports
Speaker: Gilles Gardner, Engineering Director, The Impulse Group
Authors: Gilles Gardner and Adam Armstrong, The Impulse Group
14:40
-
Topside end fittings of unbonded flexible risers are designed with annulus vent ports that serve two purposes; to safely vent permeated annulus gases and to allow integrity testing of the outer sheath. If these vent ports become blocked, annulus testing cannot be carried out and the build-up of gas has potential to rupture the outer sheath allowing seawater to flood the annulus resulting in corrosion of the structural steel components of the riser.
The Impulse Group has developed a method of inspection which utilises a small diameter articulating camera system that can be manipulated to travel through the annulus vent port tubing providing valuable insight into its condition. This method allows the full inspection of the vent port tubing to identify any debris or tube compression preventing gas release, allowing The Impulse Group to consider methods of repair to any blocked ports and re-establish a topside connection either by mechanical means or simply utilising a vacuum attachment. Application of various external fixtures also makes it possible to articulate the camera to the end of the vent port to inspect for localised corrosion of structural wires within the end fitting region resulting in detection of cracking and corrosion within the riser structural layers.
This paper describes the development and offshore deployment of the annulus vent port camera inspection system, cleaning of the vent port tubing and presents sample findings.
15:10
Networking break
SESSION 8: LATERAL BUCKLING DESIGN CONSIDERATIONS
Lateral buckling design using conditional soil friction distributions
Speaker: Ismael Ripoll, Senior Advanced Analysis Lead, Xodus Group
Authors: Ismael Ripoll, Xodus Group - Carlos Sicilia and Emilien Bonnet, TotalEnergies
15:30
-
Operation at temperature and pressure of exposed subsea pipelines results in effective axial forces which may cause lateral buckling. To perform the lateral buckling design, the subsea pipeline industry typically uses a combination of Monte-Carlo simulations and finite element analysis (FEA). The Monte-Carlo simulations are used to determine the longest virtual anchor spacing that can be reliably guaranteed (characteristic VAS), and FEA is used to determine the longest VAS with acceptable mechanical conditions (tolerable VAS). The lateral buckling design then needs to ensure that the characteristic is less than the tolerable VAS.
In this context, this paper presents a Monte-Carlo algorithm which determines the soil friction distributions conditional to buckling, and then an approach in which the tolerable VAS is in turn determined using these conditional soil friction distributions. For pipelines in which the soil friction distributions provided by the geotechnical specialists do not always lead to buckling, the proposed approach may have a significant impact on the overall lateral buckling design.
Effect of axial force on the pipeline burst resistance
Speaker: Chris Cooper, Technical Authority – Rigid Pipelines, TechnipFMC
Authors: Chris Cooper and Piotr Krawczyk, TechnipFMC
16:00
-
Engineers have been calculating the wall thickness of pipelines for years. It is often one of the first tasks to be undertaken in the design process and the initial calculation for pipe wall sizing to protect against the burst limit state is often considered to be one of the most straight forward tasks. DNV-ST-F101 provides an easy-to-use analytical equation to determine the burst resistance. However, it also includes a clause, which until very recently, has not been widely understood and therefore, rarely used in pipeline design. This clause requires the engineer to consider the effect of compressive true wall force on the burst resistance. Applying this clause is far from straight forward and has been the subject of considerable debate on a few recent projects. This paper provides an overview of the problem, before summarising an approach that may be adopted to address this code requirement. A few case studies are presented, and some practical implications discussed.
16:30
Chairman’s closing remarks